The use of banana fibre in the textile industry marks a significant shift towards sustainability and environmental responsibility. Extracted from the pseudostem of the banana plant, this natural fibre is emerging as both a substitute and a supportive element in fabric manufacturing, offering a range of versatile applications.
Extraction and Preparation:
Sustainable Alternatives:
Silk Substitute: Inner banana fibres, known as Musa textilis, are soft and lustrous, providing an eco-friendly alternative to traditional silk. Their natural sheen and texture offer the elegance of silk without its environmental footprint.
Cotton Competitor: With superior tensile strength, banana fibre is an excellent contender for producing everyday garments such as shirts, trousers, and activewear. Its breathability and moisture-wicking properties contribute to the comfort of the fabric.
Enhancing Textiles:
Blending for Durability: Blending banana fibre with other natural fibres like cotton, linen, or even with recycled polyester creates strong, sustainable fabrics. This enhances the durability and functionality of the textiles, while reducing the reliance on synthetic materials.
Texture and Aesthetics: Banana fibre yarn adds unique texture and visual appeal to fabrics. Its subtle sheen and natural variations add depth to textiles, making them suitable for a wide range of applications, including home furnishings and upholstery.
Diverse Applications:
Banana fibre’s versatility extends beyond traditional clothing. Its robust and water-resistant nature makes it suitable for sustainable bags and totes, Home decor items such as rugs, mats, and wall hangings, Industrial uses in filtration systems, soundproofing materials, and composite boards.
Impact on Sustainability:
The incorporation of banana fibre in the textile industry is a positive move towards environmental sustainability. It offers an alternative to resource-intensive materials like cotton and synthetic fibres. The use of banana fibre also promotes the circular economy by utilizing agricultural waste products, contributing to the overall reduction of environmental impact.
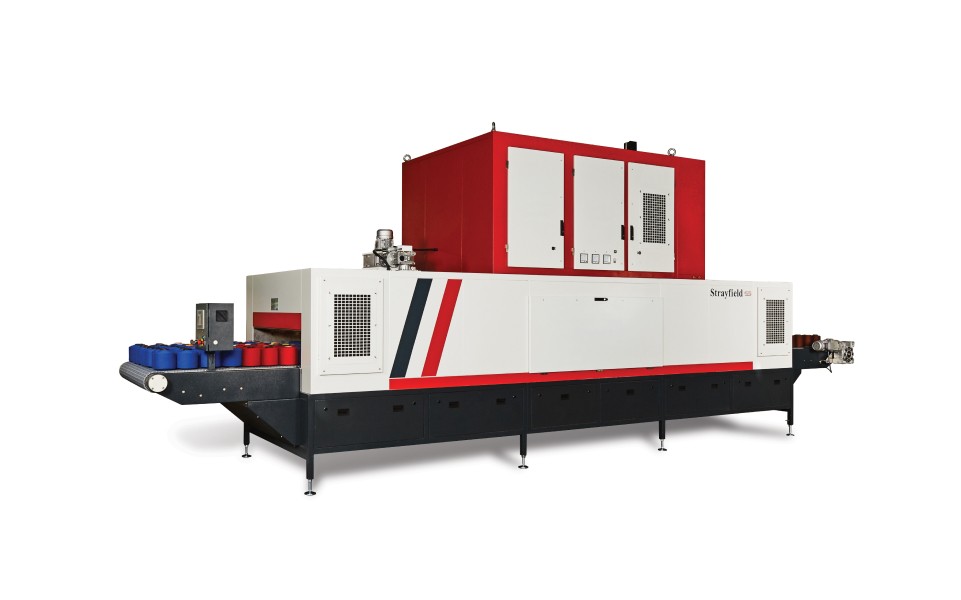
Scaling Production with Radio Frequency Dryers:
Advantages of RF Drying in Banana Fibre Processing:
Efficiency in Drying: RF dryers use radio frequency energy to heat and dry materials. This method is more efficient than traditional drying techniques, as it heats the material uniformly and quickly. This is particularly beneficial for banana fibres, ensuring consistent drying throughout the batch.
Quality Preservation: One of the challenges in drying natural fibres is maintaining their intrinsic qualities. RF drying minimizes the risk of over-drying or uneven drying, which can compromise the fibre’s strength and texture. This method preserves the natural characteristics of banana fibres, such as their tensile strength and luster.
Scalability: Strayfield’s RF dryers are designed to handle large volumes, making them ideal for scaling up production. They can accommodate increased quantities of banana fibres, facilitating larger production runs without sacrificing drying quality or efficiency.
Environmental Impact: RF dryers operate entirely on electricity and do not rely on fossil fuels to fire up boilers or chemicals to aid in processes. This contributes to a lower environmental footprint. By using purely electrical energy, they can potentially complement the eco-friendly nature of banana fibre production, thereby enhancing the overall sustainability of the process.
Implications for the Textile Industry:
The integration of Strayfield’s RF dryers into textile processing lines has been the norm for many years, and their importance or value in banana fibre processing may be no different. They have the potential to revolutionize the industry by increasing production capacity while maintaining the ecological and quality advantages of the fibre. This aligns with the growing demand for sustainable textile materials and supports the industry’s shift towards more environmentally responsible manufacturing practices.
In summary, the use of Strayfield’s RF dryers, offers a compelling solution for scaling up banana fibre production. It ensures efficiency, quality preservation, and sustainability, making it a pivotal technology in the advancement of eco-friendly textile manufacturing.